Adhesion additives have revolutionized industries that rely heavily on coatings and paints by enhancing their adhesive properties. These specialized additives are engineered to improve the bonding between coatings and substrates, ensuring durability and improved performance. The demand for such additives is growing as industries seek coating solutions that not only protect surfaces but also withstand environmental and mechanical stresses.
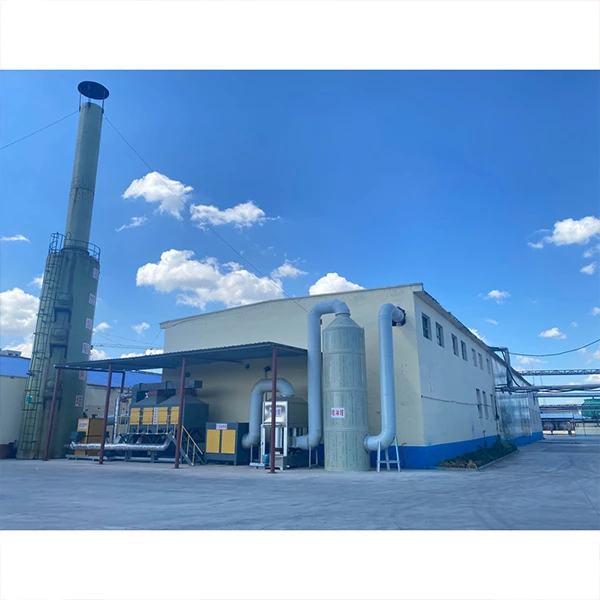
In the coating industry, adhesion is a critical property that determines the longevity and effectiveness of a surface treatment. Adhesion additives are formulated with advanced chemical compositions to interact with both the substrate and the coating material. They achieve this by altering the surface characteristics of either or both, facilitating a stronger bond. By enhancing adhesion, these additives extend the lifespan of coatings, reduce repairs, and increase the overall efficiency of the application process.
Industries such as automotive, aerospace, construction, and marine have particularly benefited from the integration of adhesion additives in their coating systems. For automotive manufacturers, these additives ensure that paints adhere better to metal surfaces, enhancing corrosion resistance and maintaining aesthetic appeal over time. Similarly, in the aerospace sector, where materials face extreme conditions, adhesion additives play a pivotal role in maintaining the integrity of protective coatings on aircraft.
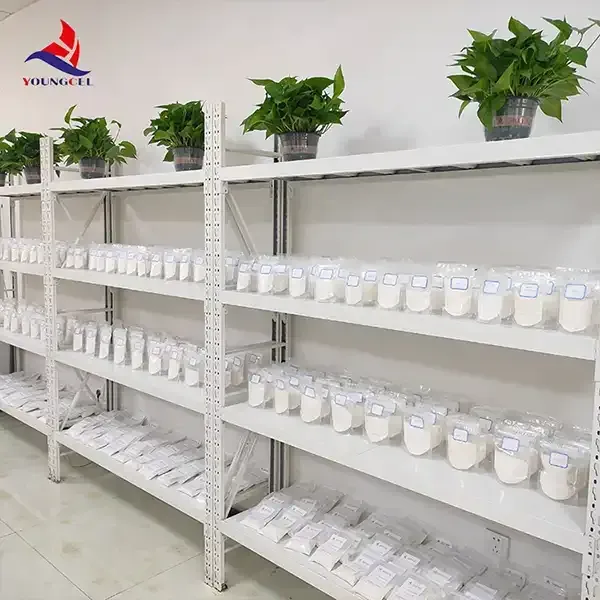
The construction industry also values these additives for their ability to help paints and sealants adhere better to building materials like concrete, wood, and metals.
This results in longer-lasting finishes and reduced maintenance costs. Additionally, marine environments pose unique challenges due to constant exposure to water and salt, making adhesion additives essential for providing robust coatings that protect vessels and offshore structures from harsh conditions.
Choosing the right adhesion additive involves understanding the specific requirements of the application, including the nature of substrates and environmental conditions. Manufacturers provide a variety of products tailored to different needs, each with unique chemical compositions and mechanisms of action. Silicone-based additives, for instance, are popular for their versatility and ability to form flexible, durable bonds with numerous substrates. Conversely, organo-functional silanes offer excellent bonding capabilities in high-temperature environments, making them suitable for industrial applications.
adhesion additive
Innovation within the adhesion additive sector is constant, driven by the need for more sustainable and environmentally friendly options. Recent advancements have focused on reducing volatile organic compounds (VOCs) in formulations to meet stringent environmental regulations. Emerging bio-based additives are also gaining attention due to their reduced environmental impact. As research progresses, it may be possible to develop additives that provide even greater adhesion while further minimizing environmental concerns.
Ensuring maximum effectiveness of adhesion additives depends on correct application processes, including surface preparation and coating techniques. Proper substrate cleaning and preparation are crucial to remove contaminants that can hinder adhesion. Similarly, the application method—whether spraying, brushing, or rolling—should be aligned with the additive’s properties to ensure uniform distribution and optimal bonding.
Expertise in the use of adhesion additives is vital, as improper application can result in suboptimal performance and potential coating failures. Professionals with knowledge and experience in both substrate materials and coating systems can significantly impact the success of applications. By leveraging their expertise, these specialists help in selecting and applying the right additives to achieve desired outcomes efficiently.
Adhesion additives are indispensable components in modern industrial coatings, contributing significantly to the performance and longevity of protective and decorative finishes across various sectors. As industries continue to evolve, so too will the technology behind these additives, ensuring their continued relevance and vital role in surface coating applications.