Wall putty and Hydroxypropyl Methylcellulose (HPMC) are integral components in modern construction and interior finishes, addressing both functional and aesthetic needs. Understanding their synergy can elevate the quality of wall finishes and enhance structural integrity.
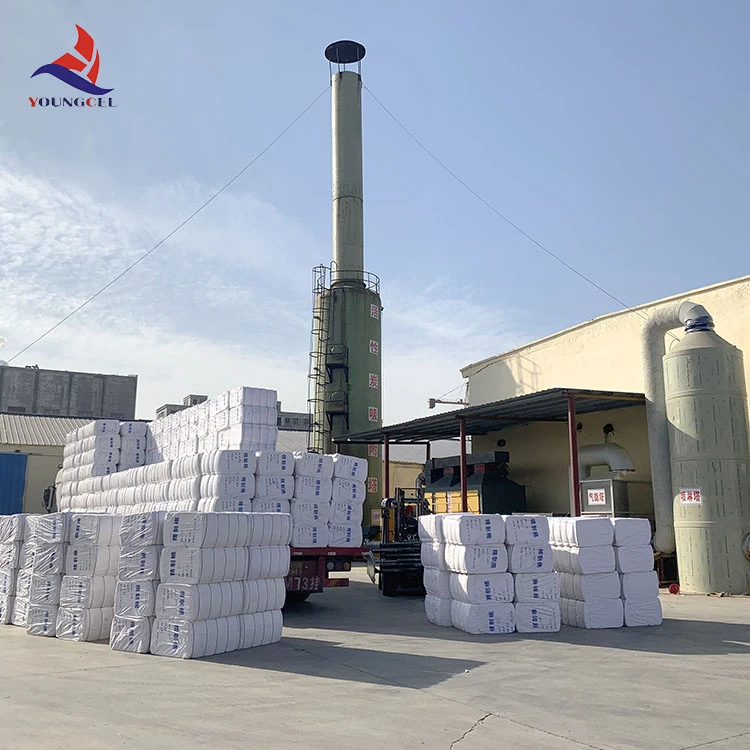
To begin, wall putty—I often describe it as the foundation for beauty on walls—serves to prepare a smooth, level base for subsequent paint applications. Its primary role is to fill unsightly dents, cracks, and imperfections on walls. Often made from white cement and blended with polymers and other minerals, wall putty ensures the longevity and durability of paintwork, providing a flawless canvas that combats moisture and resists flaking.
Here enters Hydroxypropyl Methylcellulose (HPMC), a critical additive in the formulation of wall putty. HPMC is primarily valued for enhancing the workability and performance of wall putty mixtures. HPMC, derived from cellulose, is a non-ionic, water-soluble polymer that serves several purposes in wall putty
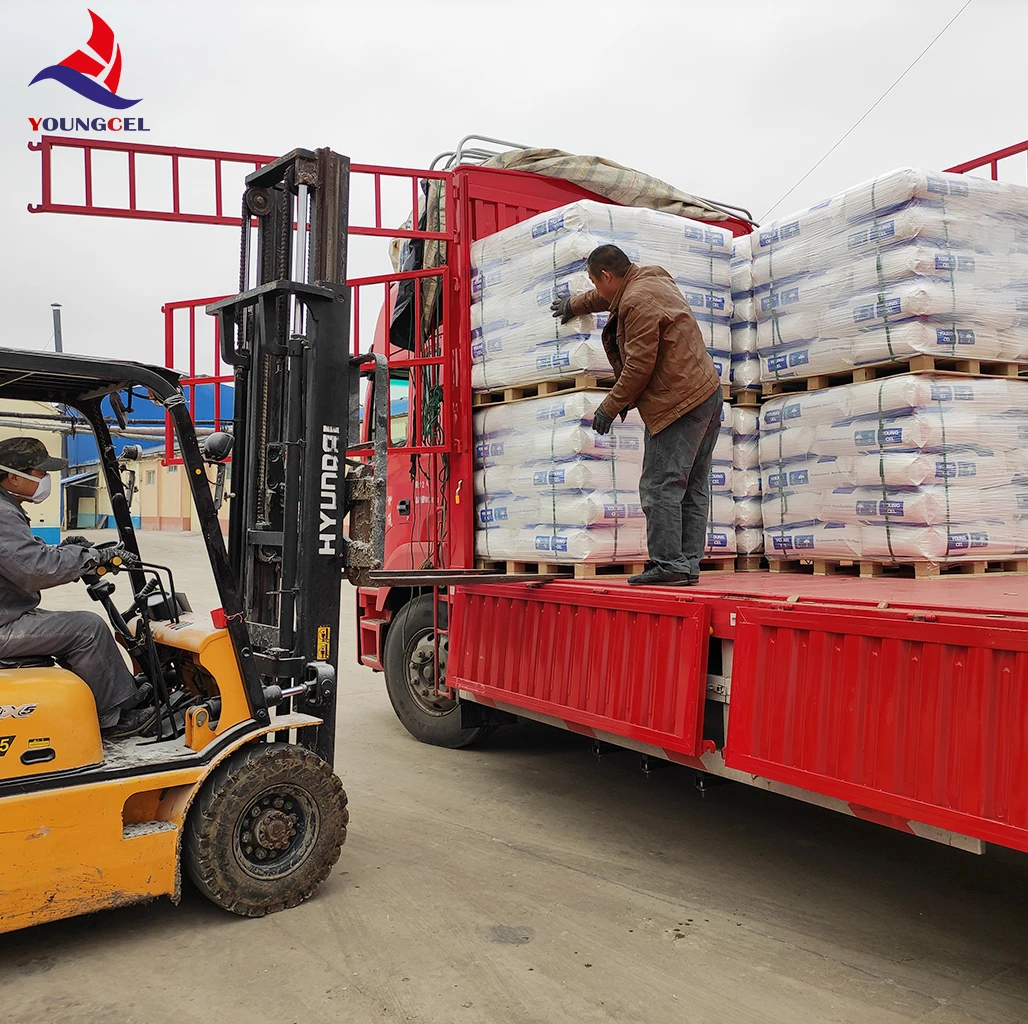
1. Improved Workability and Consistency With its thickening and thixotropic properties, HPMC moderately increases the viscosity of the putty, giving it a creamier, smoother spread on wall surfaces. This consistency is essential for achieving uniform application, reducing labor time while enhancing finish quality.
2. Water Retention HPMC possesses excellent water retention capabilities. It ensures that the moisture within the putty doesn't evaporate prematurely, allowing for extended working time and reducing the chances of cracks in the putty layer. This property is particularly vital in hot and arid climates, where rapid drying can lead to compromised surface integrity.
3.
Increased Adhesion When wall putty is enhanced with HPMC, its adhesion properties are significantly boosted. This ensures that once applied, the putty binds strongly to the wall substrate, providing a stable layer that adheres well with paint over time.
wall putti hpmc
4. Resistance to Sagging Particularly on vertical surfaces, sagging can be a common issue, compromising the visual uniformity and effectiveness of wall putty application. The intelligent incorporation of HPMC mitigates this risk, allowing even application across large surface areas.
Drawing from experiences in practical applications, the blending of wall putty with HPMC is simple and straightforward but necessitates careful measurement and mixing. Professionals recommend utilizing specific formulations that align with project needs, whether they are interior or exterior applications, to maximize benefits.
Adopting best practices in preparing and applying wall putty that includes HPMC can decisively impact project outcomes. Experts stress the importance of surface preparation before application—removing dust, loose old paint, and dirt to ensure optimal adherence and finish.
In the field, professionals often tailor the ratio of HPMC depending on specific project requirements or environmental conditions. Such expertise underlines how versatility in construction materials can address unique challenges faced in distinct locales.
For those seeking quality assurance, selecting wall putty containing certified HPMC with known origin and quality standards can establish trust and reliability in the materials used. This choice impacts not just the immediate aesthetic result but also dictates the long-term preservation of both residential and commercial properties.
Ultimately, the combined use of wall putty and HPMC exemplifies innovation in materials science, bringing together technological advancement and traditional craftsmanship. With all this know-how expertly applied, achieving wall finishes that stand the test of time—resistant to chips, cracks, and degradation—becomes less of a challenge and more an expected outcome. Pursuing sustainability, efficiency, and high aesthetic standards with these materials reflects a deep understanding of both construction science and artistic finesse, a formula that stands prominent in the modern builder’s toolkit.