In the rapidly evolving world of construction and civil engineering, the quest for materials that enhance the performance, durability, and sustainability of structures is relentless. Cement, a fundamental component in building, is no exception to this trend. The use of additives for cement has become a prominent focus, unlocking innovative avenues to elevate the inherent qualities of traditional cement mixes.
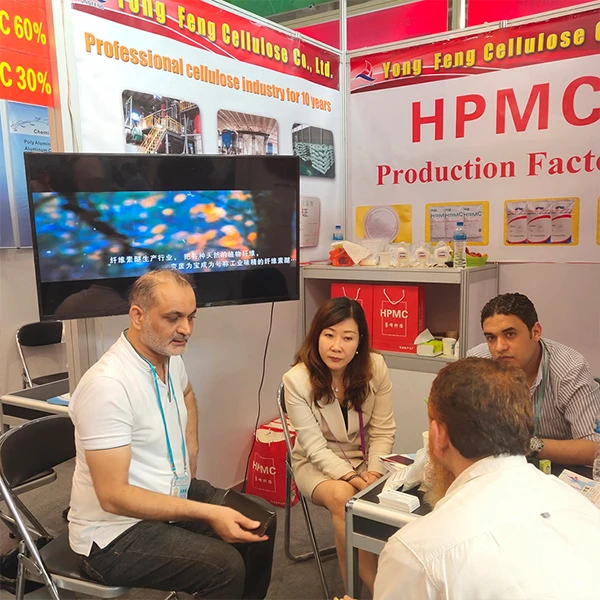
Additives for cement transcend the traditional roles of mere fillers or cost-saving materials. In contemporary applications, they play critical roles in modifying the workability, setting time, durability, and even the environmental footprint of cement. These enhancements are particularly crucial in environments subject to extreme temperatures, corrosive chemicals, or severe mechanical stress.
From a professional standpoint, the strategic incorporation of additives into cement mixtures involves deep expertise in material science. Superplasticizers, for example, are a class of additives that significantly improve the flow characteristics of cement without compromising the water-to-cement ratio. This transformation permits the crafting of high-strength concretes necessary for skyscrapers and mega-structures, maintaining structural integrity while optimizing materials' logistical and economic aspects.
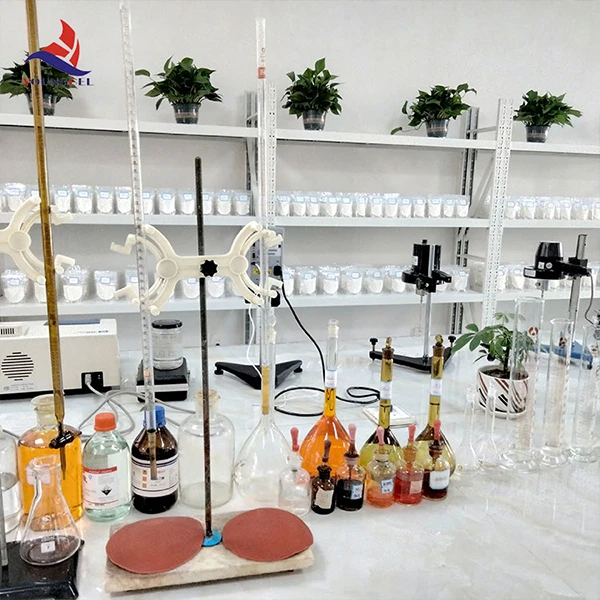
Furthermore, silica fume, an industrial byproduct, stands as a remarkable cement additive. It's characterized by its ultra-fine particles, which enhance the mechanical and chemical properties of concrete. By integrating silica fume, engineers have achieved increased compressive strength and superior resistance to aggressive chemical attacks, such as chlorides and sulfates, pivotal for marine and coastal construction projects.
The environmental impact of construction materials is increasingly scrutinized as the world pivots towards sustainable practices.
Additives offer pathways to more eco-friendly cement formulations. Ground granulated blast-furnace slag (GGBS) and fly ash, both industrial byproducts, have proven to reduce the clinker content required in cement production, subsequently lowering carbon emissions. These additives not only improve the sustainability of cement but also impart enhanced durability and reduced heat of hydration, contributing to more energy-efficient building practices.
additive for cement
Attention to trustworthiness and authority is paramount when selecting and applying cement additives. It demands manufacturers and engineers collaborate closely to understand the distinctive chemistry and performance attributes these materials bring. Relying on peer-reviewed research, verified industry standards, and cross-disciplinary innovations ensures that the integration of additives is both scientifically sound and aligned with project demands.
In real-world applications, documenting the effectiveness and reliability of cement additives requires a testimonial backbone drawn from demonstrated projects and industry benchmarks. Case studies showcasing successful implementations where additives reduced construction time, costs while enhancing structure longevity bolster confidence among stakeholders in adopting these advanced materials.
Every additive brings its unique benefits and challenges, thus necessitating rigorous testing to customize its application for each project. The journey from laboratory to application is marked by meticulous trials and recalibrations, ensuring that every innovation aligns seamlessly with the precise targets of the construction project—be it seismic resilience, thermal insulation, or rapid set times for critical repairs.
A forward-looking strategy in the adoption of cement additives embraces technological advancements and cross-sector knowledge sharing. By fostering a culture of continuous learning and development, the construction industry is poised not only to meet the ever-expanding performance criteria of modern infrastructure but also to pave the way for a sustainable, resilient future.