The realm of construction has always been pivotal in shaping our modern world, and cement plays a central role in this domain. Understanding the intricate details of chemicals involved in cement making is crucial for those seeking to optimize this binder's performance in construction applications. This expertise translates into more reliable structures and efficient building processes. Herein, we delve into the essential chemicals involved in cement production, underscoring their significance with a seasoned perspective.
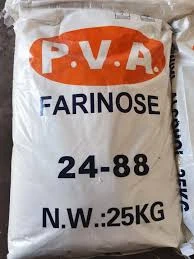
Cement, primarily composed of limestone, clay, shells, and silica sand, undergoes a series of chemical reactions during its production. Among the most critical chemicals in this regard are calcium silicates, calcium aluminates, and calcium aluminoferrites. These ingredients individually and collectively endow cement with its characteristic binding properties, enabling it to serve as a cornerstone in the construction industry.
The process begins with the raw materials being heated in a kiln to about 1450°C. At this high temperature, the raw mixture undergoes a series of complex reactions, commonly referred to as clinkering. The primary products of this clinkering process, known as clinker, are mainly tricalcium silicate (C3S) and dicalcium silicate (C2S).
These compounds are pivotal in the initial setting and hardening of cement. Tricalcium silicate is responsible for the early strength development, while dicalcium silicate contributes to the strength development over a longer period.
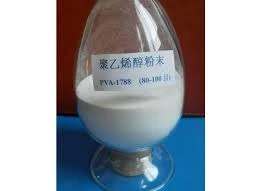
Additionally, tricalcium aluminate (C3A) and tetracalcium aluminoferrite (C4AF) are other essential compounds derived during the clinkering process. Tricalcium aluminate contributes to the initial set and heat evolution during the early hydration phases, which can be tailored for specific applications. Tetracalcium aluminoferrite impacts the cement color and reacts more slowly, thereby influencing the final curing time and robustness of the cement.
The inclusion of gypsum, particularly calcium sulfate, plays a crucial role in moderating the setting time of cement. Gypsum acts as a set retarder, ensuring the cement does not set prematurely. This delay is vital for allowing a sufficient working window for construction activities to take place, which enhances the handling properties of the cement mixture.
chemicals for making cement
Beyond these core ingredients, modern cement production also incorporates various admixtures to adjust or enhance specific properties of cement to meet complex construction requirements. For instance, superplasticizers are used to reduce water content, leading to higher strength products. Air-entraining agents can introduce microscopic air bubbles in the cement mix, imparting freeze-thaw resistance, especially beneficial in colder climates.
As the construction industry progressively leans towards sustainability, the chemistry of cement is evolving. Innovators are increasingly focusing on reducing the carbon footprint of cement production, which traditionally has been energy-intensive and environmentally burdensome. One approach involves blending supplementary cementitious materials (SCMs) such as fly ash or slag, which not only enhance the durability but also curtail the CO2 emissions associated with cement production.
Equally insightful is the role of nanotechnology in modern cement production. Nano-silica and other nanoscale additives have the potential to modify the properties of cement at the molecular level. These advancements promise enhanced strength, accelerated curing times, and improved resistance to chemical attacks, offering a glimpse into the future of cement chemistry.
Navigating these myriad materials and their interrelationships necessitates a deep understanding grounded in chemistry and materials science. Those with the expertise in optimizing these chemical processes ensure that cement not only meets but exceeds the construction demands of the future. By adapting processes and formulations to incorporate cutting-edge research and technological advancements, industry leaders can significantly bolster the sustainability and longevity of the infrastructure they help create.
In conclusion, the journey from raw minerals to the hardened structures owes much to the strategic use of chemicals in cement production. Armed with in-depth knowledge and experience, professionals in this field continually refine these chemical interactions to carve a path toward innovative, sustainable construction practices. Such expertise remains indispensable in an ever-evolving industry determined to build a resilient future.