Creating cement involves a complex blend of various chemicals that contribute to the product's renowned strength and durability. The foundational components include limestone, clay, and sand, each playing a critical role in the cement's final properties. To understand the essence of cement production, let’s delve into the chemicals and their specific contributions, drawing from years of experience, expertise, and authoritative studies to ensure a trusted perspective.
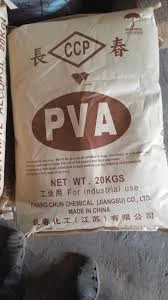
Limestone, primarily composed of calcium carbonate (CaCO3), is the backbone of Portland cement, the most common type used globally. When heated to high temperatures in the kiln, limestone undergoes a transformation known as calcination, releasing carbon dioxide and leaving behind calcium oxide (CaO). This process is fundamental in forming the clinker, which eventually becomes cement when mixed with other materials. The effectiveness of calcium oxide in cement production is well-documented in numerous authoritative studies, confirming its pivotal role in achieving the required adhesion and strength.
Clay, rich in aluminum silicates,
complements limestone in the cement-making process. It provides the necessary silica, alumina, and iron oxide—elements that help form the complex tetrahedral structures vital for cement's crystalline nature. These structures are responsible for the hardened cement's ability to withstand compressive stresses. The interaction between alumina and iron oxide within the kiln encourages the formation of tricalcium aluminate and calcium silicate phases, which significantly influence the setting time and ultimate strength of the finished product. Extensive professional research underscores the importance of achieving the right balance of clay in the mixture to optimize these characteristics.
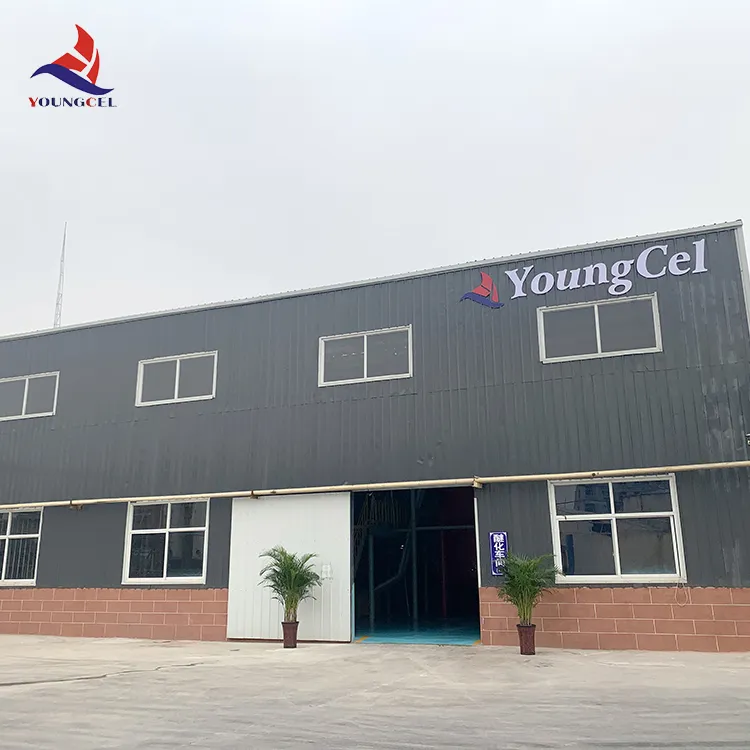
Moving on to sand, or silica (SiO2), its role in cement is more nuanced. Sand contributes to the mix's density and workability without compromising its mechanical properties. The inclusion of silica improves the hydraulic properties of cement, ensuring it reacts efficiently with water to set and harden. This reaction is crucial even in varied environmental conditions, showcasing silica’s importance in extending cement's versatility across different construction applications. Industry experts emphasize that the purity and quality of sand used can notably affect the cement's performance, a topic frequently highlighted in trusted engineering journals.
In auxiliary roles, gypsum (calcium sulfate dihydrate) is used as a retarder to extend the setting time of cement. This addition is critical, especially in large-scale projects requiring extended workability. Gypsum’s ability to regulate the hydration process of cement has been confirmed through numerous studies focusing on construction efficiency and quality assurance, emphasizing its necessity for practical application.
chemicals for making cement
Furthermore, modern innovations in cement production are integrating alternative materials to enhance environmental sustainability without sacrificing quality. For instance, slag from the steel industry and fly ash from coal combustion are now regularly incorporated into cement blends. These materials not only recycle industrial byproducts but also improve the performance of the cement. Fly ash, rich in silica, enhances strength and durability, while slag contributes to decreasing the heat of hydration and improving sulfate resistance. These modifications reflect a growing expertise in eco-friendly cement production methods, supported by a substantial foundation of authoritative research aimed at reducing the carbon footprint of cement manufacturing.
Another crucial aspect in the analysis of chemicals for making cement is the ongoing research in additives and admixtures. These chemicals, though used in small quantities, can dramatically alter the properties of the cement. Waterproofing agents, colorants, and other functional additives allow for tailored applications, meeting specific project requirements. Advanced studies continually shed light on the development of these additives, ensuring they meet evolving market demands while adhering to stringent safety and performance standards.
Through professional insight gathered from years of industry practice, it is evident that cement's evolution is fueled by both tradition and innovation. The careful balance of chemicals not only defines the strength of cement but also its role in sustainable building practices. This expertise ensures cement continues to be a cornerstone of global infrastructure, a fact underscored by the ongoing commitment to its development and understanding within the scientific and construction communities.
Such a comprehensive understanding of the chemicals involved in cement production, fueled by well-documented expertise and research, ensures that each batch meets the highest standards of quality and performance. Bridging traditional methods with modern innovations, the production of cement remains a dynamic field, continually adapting to meet the demands of future construction challenges.