The Economics of Cellulose Ether Price
Cellulose ether, a versatile derivative of cellulose, is a crucial component in various industries ranging from construction to pharmaceuticals. Its price is influenced by a myriad of factors that contribute to its overall market value. This article delves into the economic considerations behind the cost of cellulose ether and how it affects downstream applications.
The primary determinant of cellulose ether price is raw material availability. Cellulose, derived mainly from wood pulp and cotton, is subject to fluctuations depending on global supply chains and environmental policies affecting forestry practices. A scarcity of cellulose sources can drive up the price of cellulose ether, making it less affordable for manufacturers who rely on it as a base ingredient.
Another significant factor is production costs, including energy expenses and labor. As cellulose ether production is energy-intensive, variations in energy prices can impact the final cost. Furthermore, labor markets and regulations also play a role; regions with higher wages or stricter industrial standards may produce cellulose ether at a higher price point than those without such constraints.
The demand for cellulose ether also influences its pricing. Industries experiencing growth, such as construction during a real estate boom or pharmaceuticals during a health crisis, will increase the demand for cellulose ether, potentially causing prices to rise. Conversely, in economic downturns or when substitute materials gain popularity, demand may decrease, leading to lower prices Conversely, in economic downturns or when substitute materials gain popularity, demand may decrease, leading to lower prices
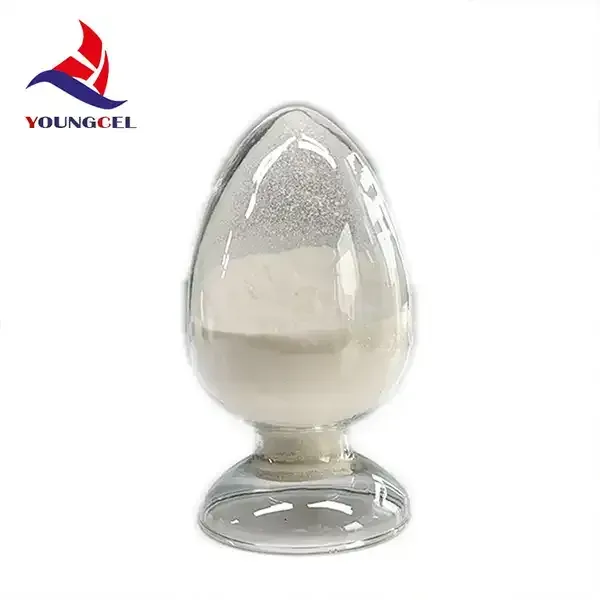
Conversely, in economic downturns or when substitute materials gain popularity, demand may decrease, leading to lower prices Conversely, in economic downturns or when substitute materials gain popularity, demand may decrease, leading to lower prices
cellulose ether price .
Transportation and logistics cannot be overlooked. The distance between production facilities and consumer markets, along with transportation costs, tariffs, and trade agreements, all contribute to the final price of cellulose ether. For example, international trade disputes can lead to import taxes that raise the cost for consumers in the affected regions.
Market competition and innovation also play significant roles. Companies vying for market share may engage in price wars, reducing costs for consumers. On the other hand, advancements in production technology can lower manufacturing costs, allowing companies to drop prices without sacrificing profit margins.
In conclusion, the price of cellulose ether is a complex interplay of raw material availability, production expenses, demand dynamics, logistical challenges, and competitive forces. It is a delicate balance that manufacturers and consumers must navigate to ensure they acquire this essential compound at a reasonable cost. As we consider the economics of cellulose ether, it becomes clear that its price is not merely a number but a reflection of broader market and global conditions.